A good lesson about failures of theoretical design and learning from practical research findings is when we observe that the shiplet won’t plunge when test-driving in open waters. After checking the software and many other possible reasons, it turns out the depth meter does not work. But it only fails when driving, what made it a bit harder to debug.
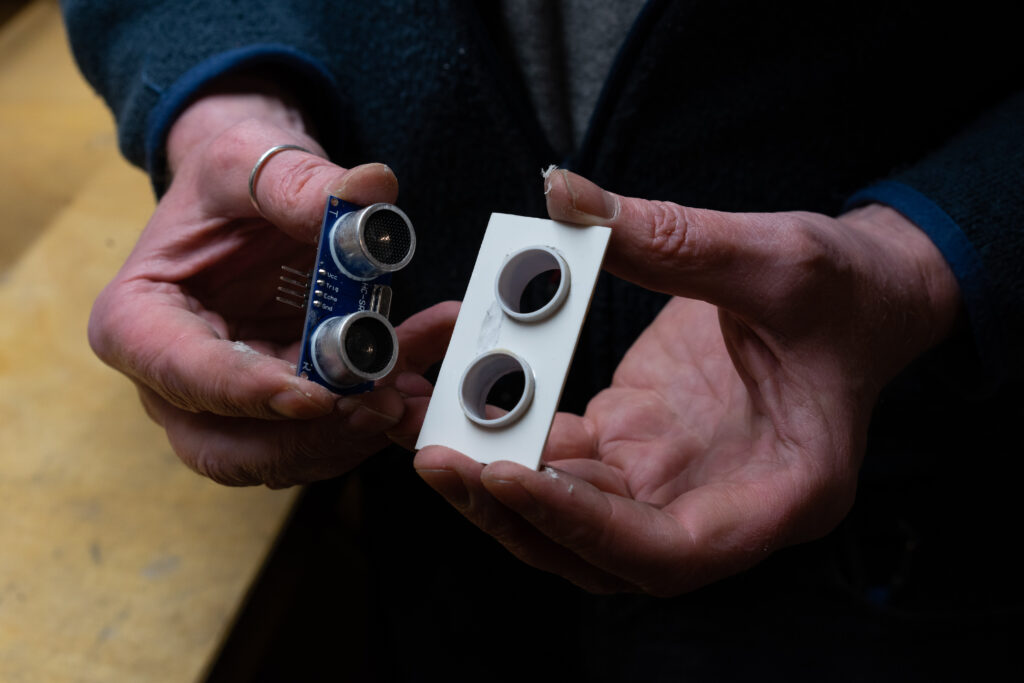
To measure the distance of the shiplet’s deck from the water surface we use an ultrasonic sensor. The sensor resides in the center of the decks underside, right behind the middle pylon, facing the water surface. It has gone through many tests in our test basin, where the sensor’s resolution of roughly 0,3 cm has proven more than good enough for our purpose. The micro processor then calculates a smoothed simple moving average of the data to distinguish, if the shiplet needs to ascend or descend or if the submerged hull is in the desired position, halfway under the water, when the deck is roughly 11 cm above the surface.

In all our stationary tests this worked pretty well, but now when we speed up in open waters the altimetry goes heywire. The ultrasonic sensor fails to receive its reflected signal from the rippling water surface. As a result the data is totally out of range and therefore useless. To fix this, we tried to position the sensor at the nose of the vessel, to avoid the tumultuous impact of the rest of the hull. But depending on speed, wind and waves the sensor’s signal capturing is far away from reliable. In the end it just seems to be the wrong approach.
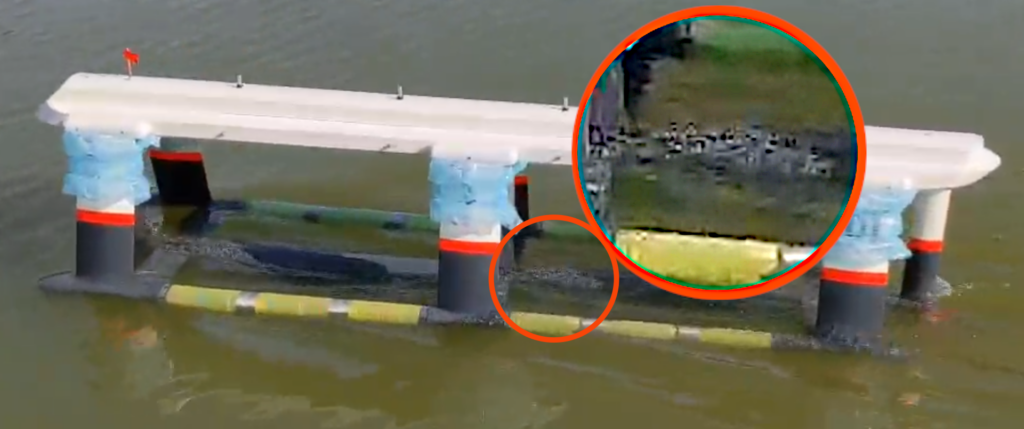
Thanks to a very fortunate circumstance we do have an alternative plan to measure the shiplets depth (and speed). Since early on we were thinking of good ways to determine the shiplets speed in the water. One promising approach was to measure the underwater pressure to the fore and aft when driving. So luckily we have provided two small pipes for that purpose when building the shiplet.
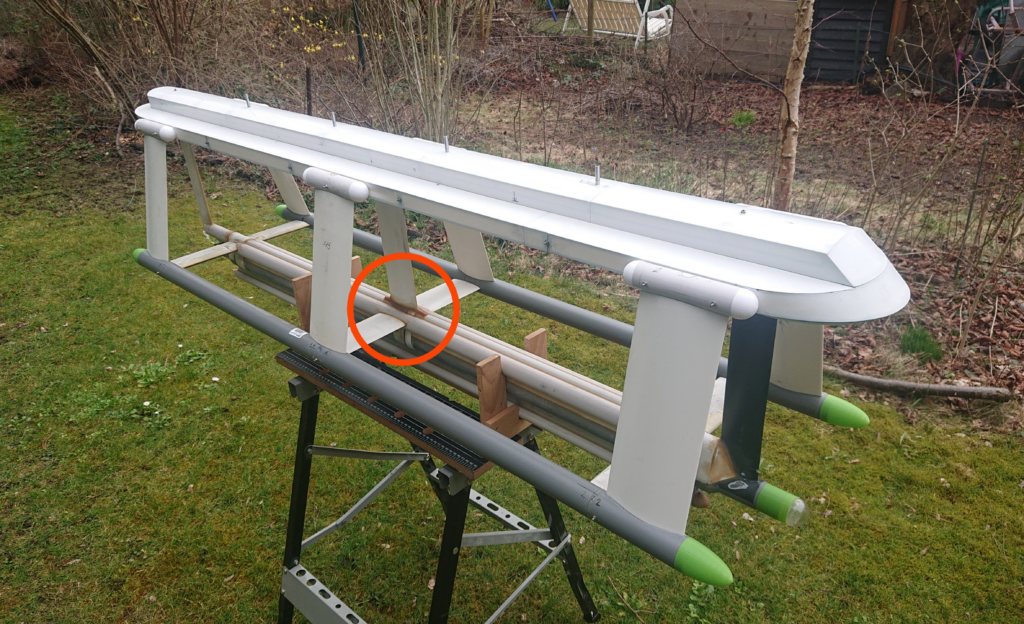
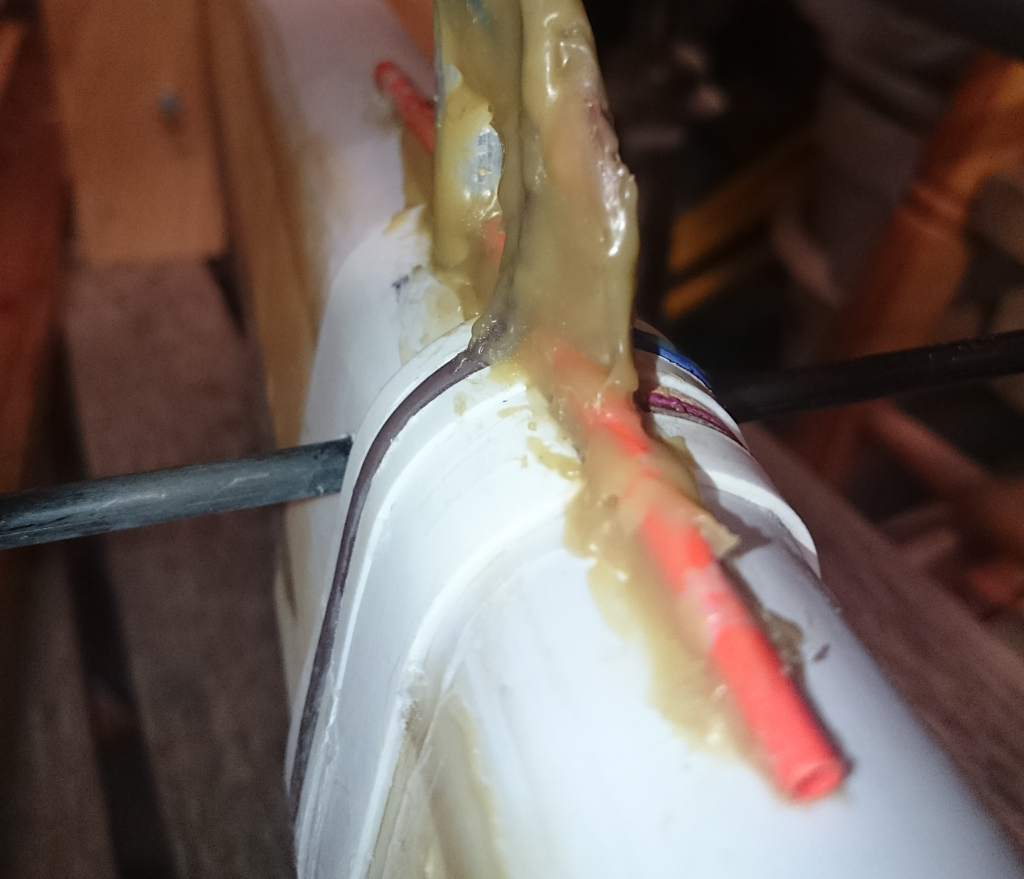
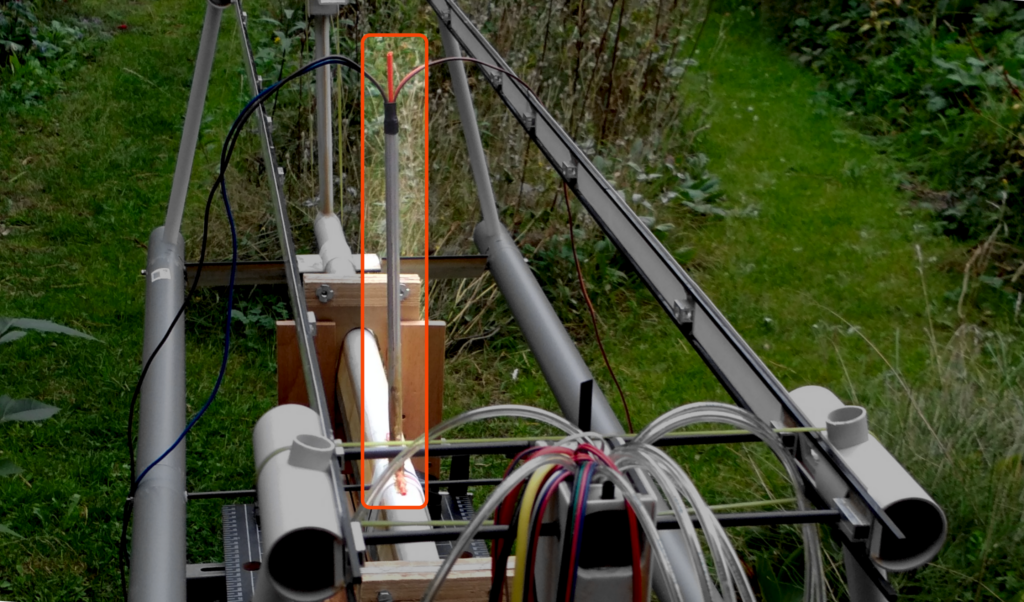
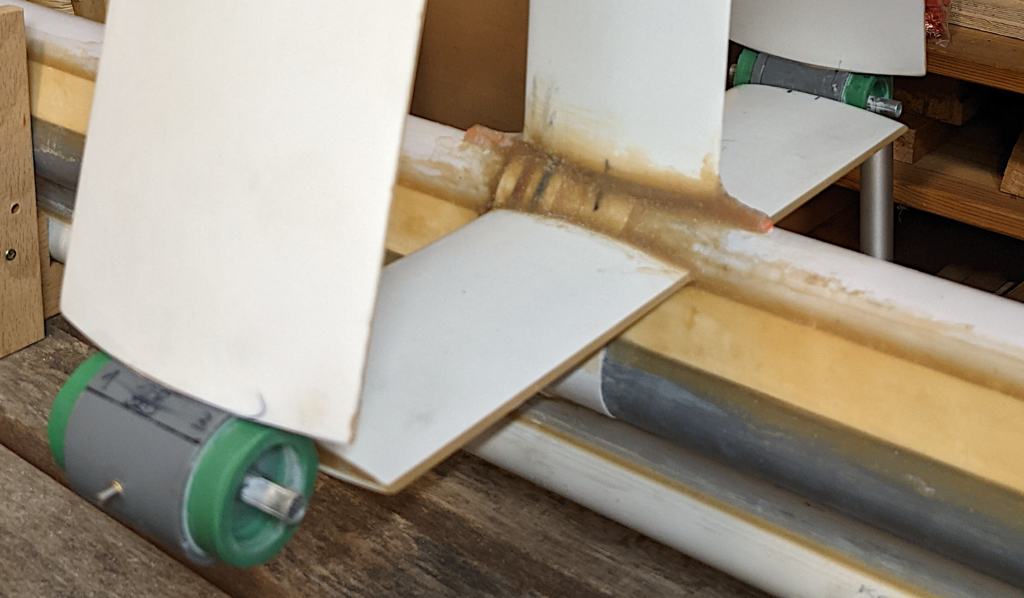
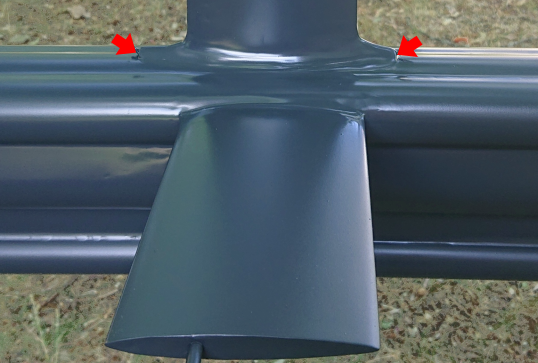
Next we need to build a pressure measuring system replacing the inapplicable ultrasonic sensor.