The shiplet’s deck is mounted on 9 fin-formed pylons, 3 edge-gated on each side connected to the under water side tubes and another three in the middle of the deck, connected to the nose, center and tail of the central hull. We also use fin-formed shapes for the flapping stabilizers and other horizontal connections.

It took us a while to figure out how to best build the fin-formed shape. Finally we ended up milling a 1,3 mm deep V-shaped 30° groove into 1,5 mm thin ABS boards. Then we fill the groove with solubilizing plastic glue and fold it until cured. Next we add a dual component acrylate adhesive glue to the open ends and put the part in our wooden molding press, which we then tighten to the desired shape. For smaller parts we also use a set of cramps. Once completely cured it results in inherently stable fin-formed parts.


Balloon Blow Pipes
The outer starboard and portside pylons in the midship section are hosting the connection between the air hoses from the upper deck with the connection pipe sockets for the balloons in the under water side-gated balast tanks. Therefore little tubes are lead through the pylons with connection pipes at their ends.

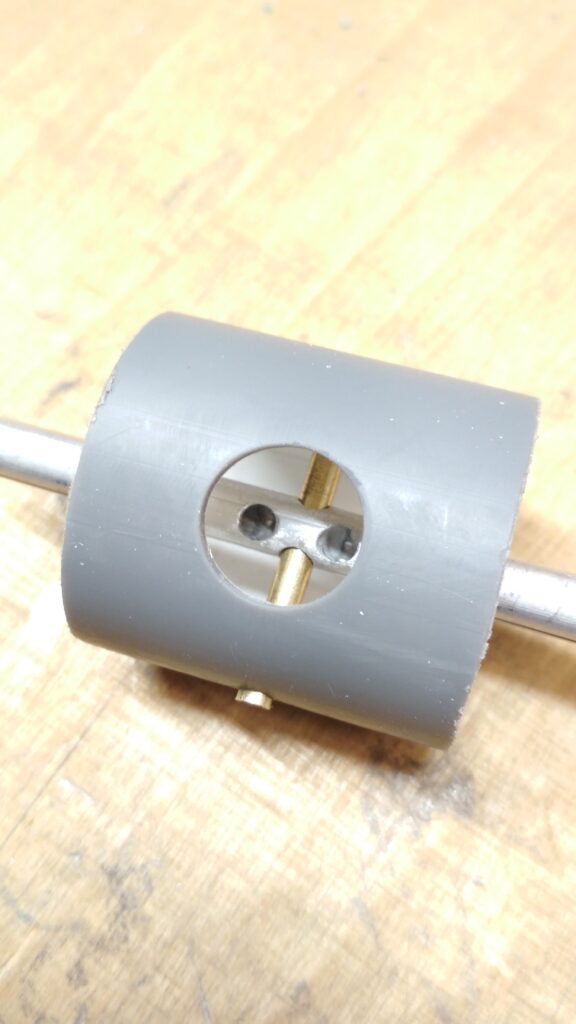



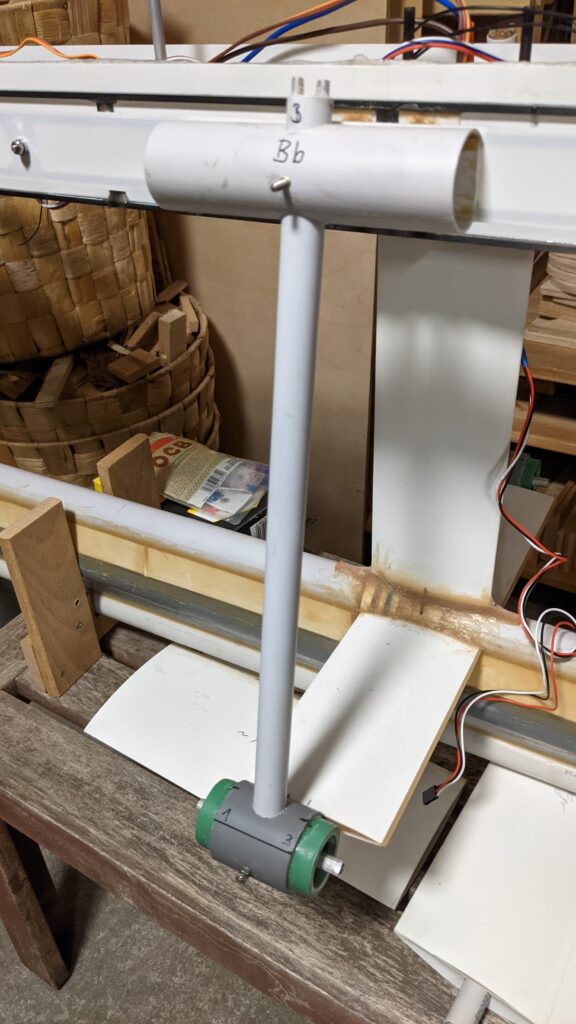
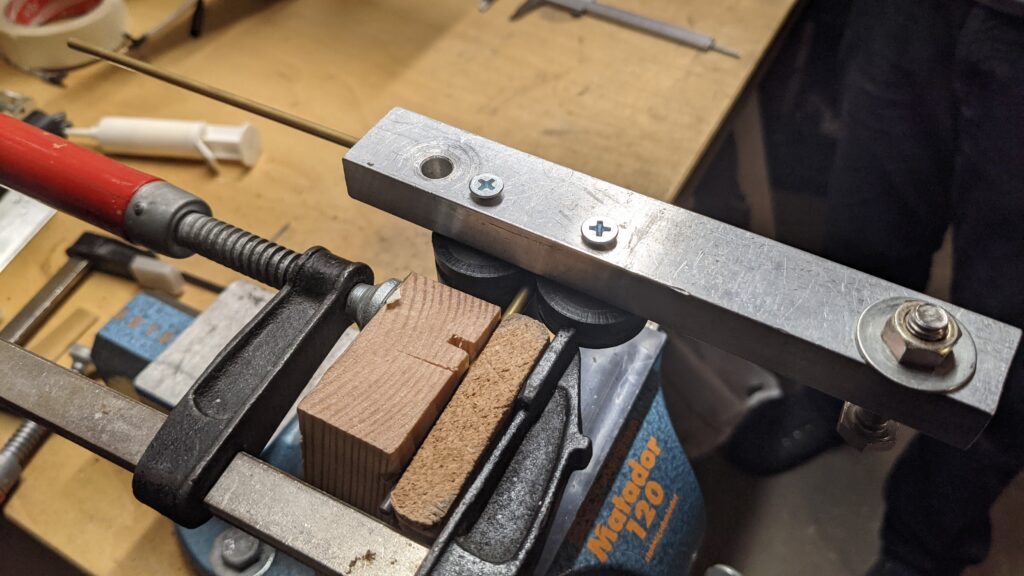

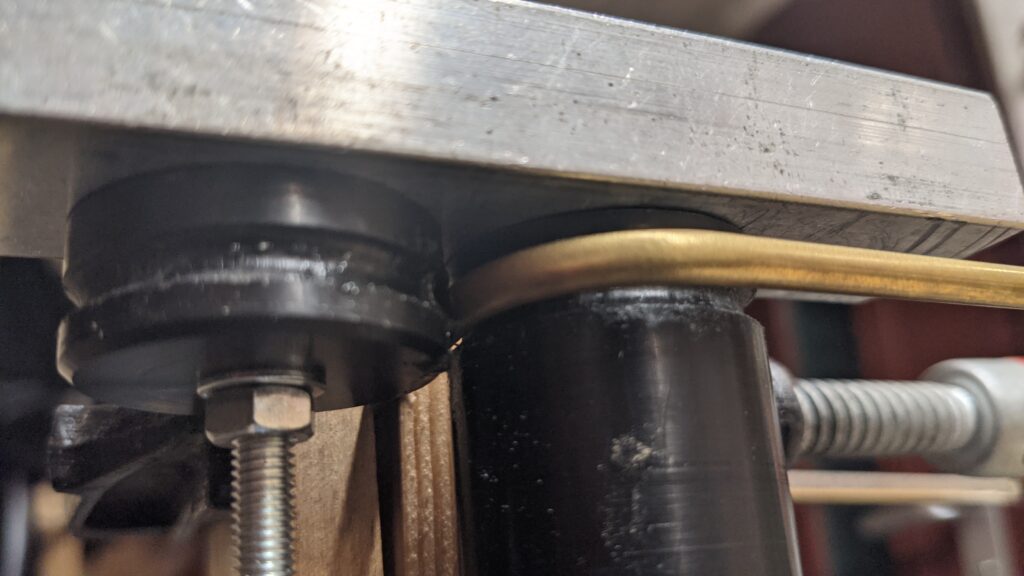





